Downstream Processing
Downstream processing applications can run into some very tough challenges. That’s why you need a partner with decades of experience and that understands how small mistakes can have big consequences. Reliability and experience are what make Flowserve your partner of choice.
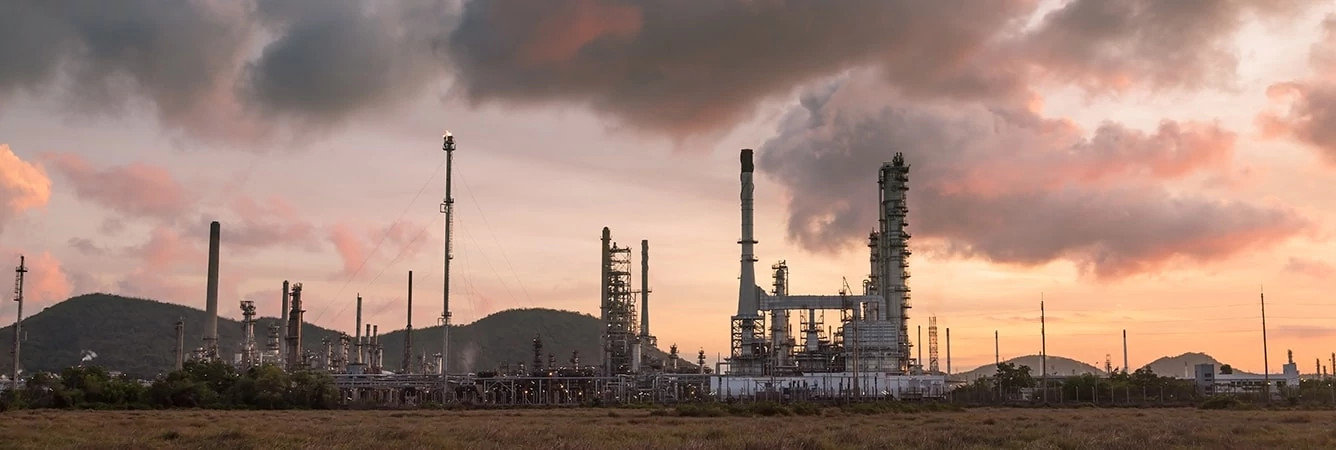
Uptime, throughput and yield
Predictability and reliability of service
Environmental and safety considerations
Your learning library
Explore Flowserve VirtualPlant:
- Tour the 3D Virtual Refinery for consolidated information on all the products we recommend.
- Explore the VirtualPlant to experience 3D models of plants in key industrial applications.
Learn about our advanced decoking system:
- Watch a series of videos to discover how our fully integrated decoking system optimizes output, increases reliability, and provides unparalleled personnel safety.
- See all of our equipment and systems for hydraulic decoking.
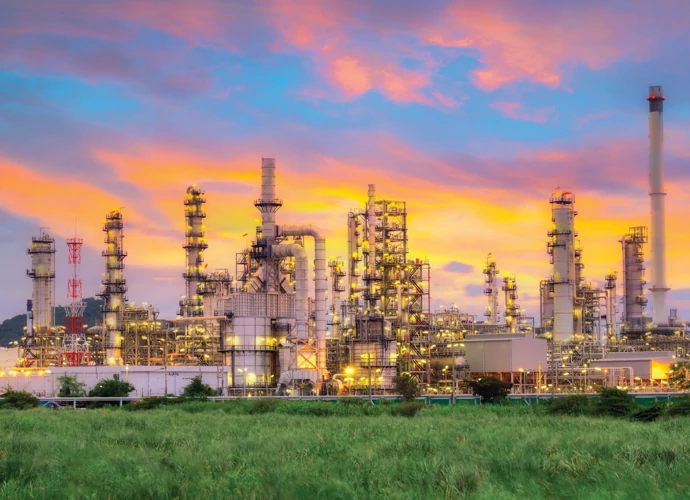
Advances in Compressor Anti-Surge Valve Design Enhance Reliability and Performance
What makes anti-surge valves reliable during downstream processing? A design that’s durable, certainly, but also that can be easily maintained and tuned in the field. Learn more about how you can lower operating costs and reduce downtime.
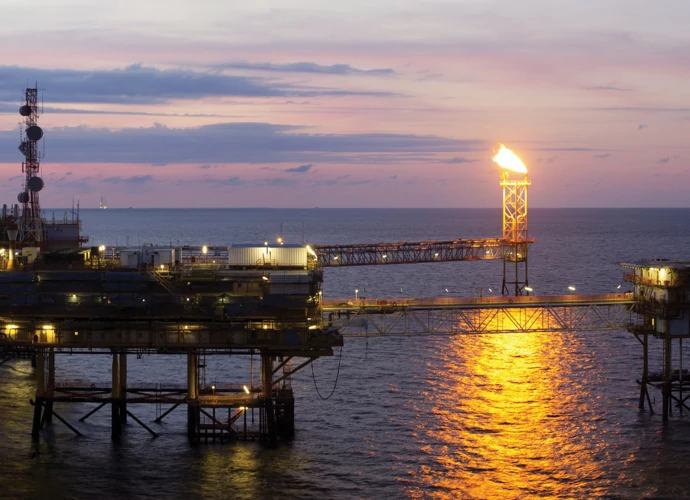
Safe and Efficient Flare Gas Recovery
In downstream applications, liquid ring compressor failures can lead to expensive downtime, environmental impacts and dangerous working conditions. Learn how to evaluate and select the right liquid ring compressors to ensure reliable, efficient and safe flare gas recovery.
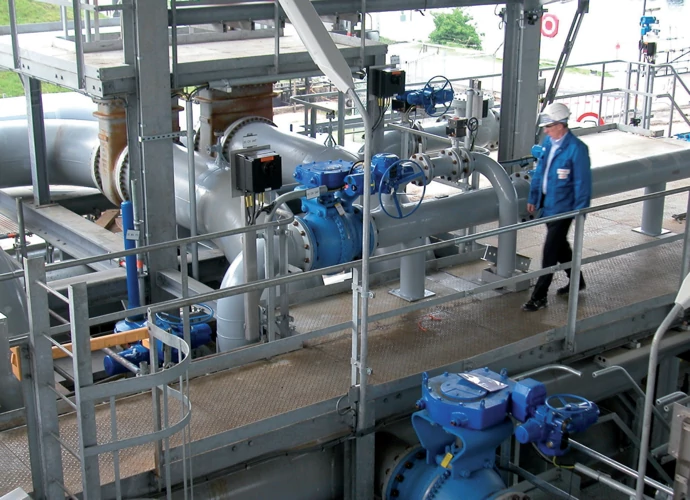
Advanced Data Processing Capabilities Make Actuators Smart
In downstream applications, valve failures bring severe and costly consequences. Smart actuators improve valve reliability, simplify maintenance, and proactively identify upset conditions before experiencing downtime.

Refinery Application Solutions Guide
A valuable reference for anyone associated with an oil refinery. This guide is written by Flowserve experts in refinery processes and details the Flowserve products best suited for providing flow control solutions to each specific plant application.
Use Cases
Much attention has been given to biomass and its modifications as a substitute for fossil fuels in the developed world. Among the modifications are biogas, alcohol, and biodiesel. Many of these operations are small independently operated facilities that Flowserve has excelled in supporting and servicing.
Flowserve offers solutions for catalytic cracking to help you exceed expectations.
Coal is one of nature’s most obdurate, but valuable, resources. Flowserve engineers have spent decades perfecting specialized equipment designs and systems for coal liquefaction applications that are durable and tough to reduce mean time between repairs.
Since the first modern delayed coking unit was installed in 1928, Flowserve has pioneered virtually every pumping technology advancement in this essential residue conversion process. Through its Worthington, IDP, Byron Jackson and Pacific heritage brands, Flowserve has become — and remains — the refining industry’s preferred partner for delayed coking process pumps and hydraulic decoking systems, with more than 200 installations worldwide.
Discover how our decoking system is fully integrated to optimize output, increase reliability, and provide unparalleled personnel safety.
See all of our equipment and systems for hydraulic decoking.
Flowserve offers solutions for distillation to help you exceed expectations.
Natural gas processing will encounter significantly more raw sour gas as the sweet crude becomes more and more scarce. The sour gas has a high content of H2S that needs to be removed and the sulfur contained.
At Flowserve, we’ve applied our long history of engineering reliable products for gas plant operations to emerging gas to liquids technology. This longstanding expertise applied to both Fischer-Tropsch and Mobile processes, enables you to capitalize on nature’s resources and improve performance with fewer pollutants.
Converting gas oils to high-grade gasoline requires extremely high temperatures and extremely high pressures. Flowserve solutions are built and engineered to withstand these tough conditions for continuous uptime and high performance. This enables you to create cleaner-burning fuels.
Hydrotreating is an established refinery process for reducing sulphur, nitrogen and aromatics while enhancing octane number, density and smoke point. Flowserve actively and successfully pursues and operates comfortably in the demanding hydrotreating applications.
When handling this crucial energy supply and tough application, you need a partner with predictable solutions. Flowserve has a successful record in LNG pipelines, liquefaction applications and the return to gas regasification process. You get predictability and reliability with the highly engineered products and global presence of Flowserve.
Flowserve provides a complete line of ISO/API, ISO/ANSI and generic service pumps and mechanical seals to handle virtually all NGL operations—from deethanization to depropranization to debutanization. Variances of temperature, pressure, and materials used throughout these techniques require the specialized engineering of an industry leader to ensure maximum efficiency. That would be Flowserve.
Refining comprises a series of increasingly brutal process steps from relatively mild vacuum and atmospheric distillation to the extremes of catalytic and thermal cracking. Equipment and materials of construction are pushed to their limits. Flowserve ensures that their reliability and safety are considered first and foremost.
The key ingredient to a successful process for this application is the ebullated bed reactor recycle pump, engineered and designed by Flowserve. Our product portfolio features this pump and other highly engineered pumps and valves that stand up to the rigors of this important process. Flowserve has a wealth of experience in this difficult application that is critical to the continuous operation in the ebulator.
Related Products
Let’s discuss your needs
Contact Us